Simplified Process Flow: Inputs, Transformations and Outputs
The H2Gen process flow leverages advanced engineering to seamlessly convert off-gas and steam into hydrogen and enriched CO2. The process is designed for efficiency, modularity and adaptability, ensuring optimal performance in diverse industrial environments.
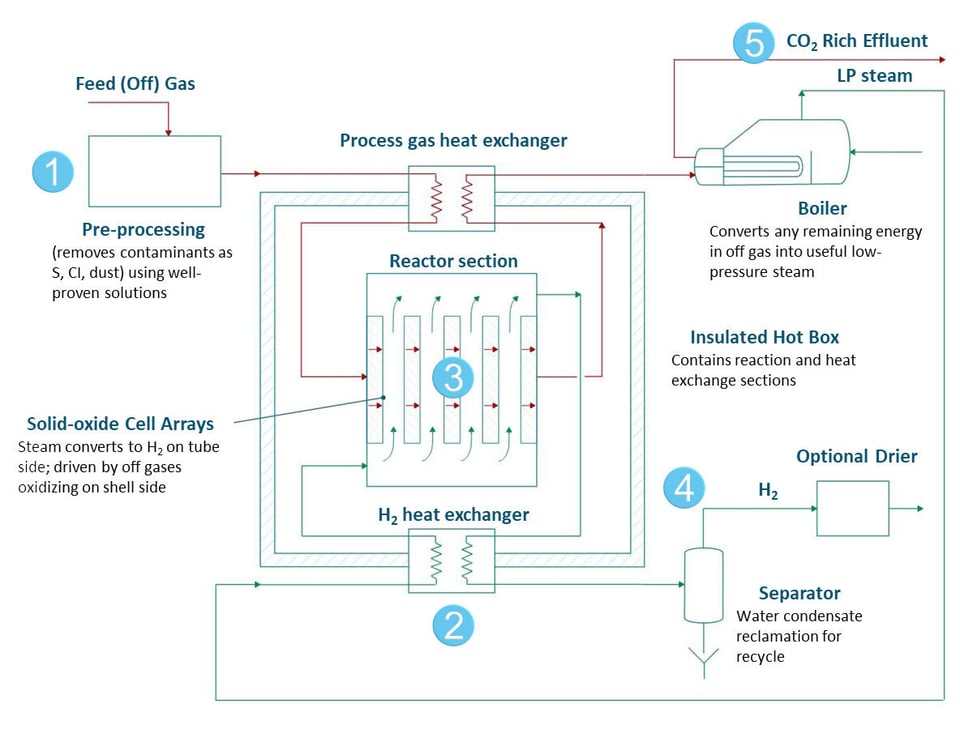
Key Process Stages:
- Off-Gas Pre-Processing: Off-gas enters the system and undergoes pre-treatment to remove particulates, moisture and contaminants. This ensures a clean feedstock for the reactor.
- Steam Integration: Water, in the form of steam, is introduced and carefully regulated to balance the reaction dynamics within the system.
- Solid Oxide Reactor: The heart of the system, this proprietary reactor uses a solid oxide membrane to facilitate the conversion of steam and off-gas into hydrogen and CO2 in a single step, without mixing the streams directly.
- Hydrogen Purification: The produced hydrogen is separated and condensed, delivering >99% purity without the need for external purification systems like PSA beds.
- Enriched CO2 Stream: A concentrated stream of CO2 exits the reactor, ready for capture or reuse, aligning with decarbonization goals.
This streamlined process allows H2Gen to deliver industry-leading performance with a smaller footprint and lower costs compared to traditional methods.
Reactor Design and Capacity: Scalable Solutions for Every Need
H2Gen’s innovative reactor design offers unmatched flexibility and efficiency, catering to a wide range of applications. From small-scale setups for biogas-to-hydrogen production to large industrial capacities, our reactors deliver exceptional performance with minimal operational costs.
Small-Scale Applications: 1-5 TPD
Single or Two-Reactor Plants: Ideal for biogas-to-mobility applications, utilizing one or two reactors for cost-efficient hydrogen production.